

The deciding factor is often the number of SMT components or through-hole components a board uses. These days solder reflow is the most common process, but wave soldering is still sometimes used for certain boards. When it’s time for your CM to manufacture your board they’re almost certainly going to use either solder reflow or wave soldering. You’ll learn more about the differences between flux and solder in the next blog in this series. If you’ve used a handheld soldering iron and solder wire the smoke you see when you melt the wire is the flux burning off. Flux can be broadly defined as a cleaning agent, which removes oxidation from the metal surfaces to be soldered. The other main ingredient in soldering is flux. Exposing board components to such high temperatures can reduce their useful lifetime and cause problems when your board is in the field. Unless regulations require you to use lead-free solder, like in the European Union, leaded solder will generally be simpler to use and has a lower risk of defects. The primary difference between the two is their melting points, with lead-free soldering usually having a melting point 50 C higher than leaded solder. Due to concerns over the toxicity of lead, unleaded or lead-free solder is becoming more common. Solder is an alloy typically composed of tin and lead however, other elements such as silver are also used. With this technique, a strong but reversible connection can be made between electrical conductors, if necessary for component replacement or board repair. The process is distinguishable from welding in that only the fused metal melts, while the two connecting metals remain undeformed. Soldering is the process of connecting two metals together by fusing them with a different element, solder. Understanding these processes and principles behind soldering will help you design to avoid the various defects that can be difficult to trace and kill a design when it’s time for production.
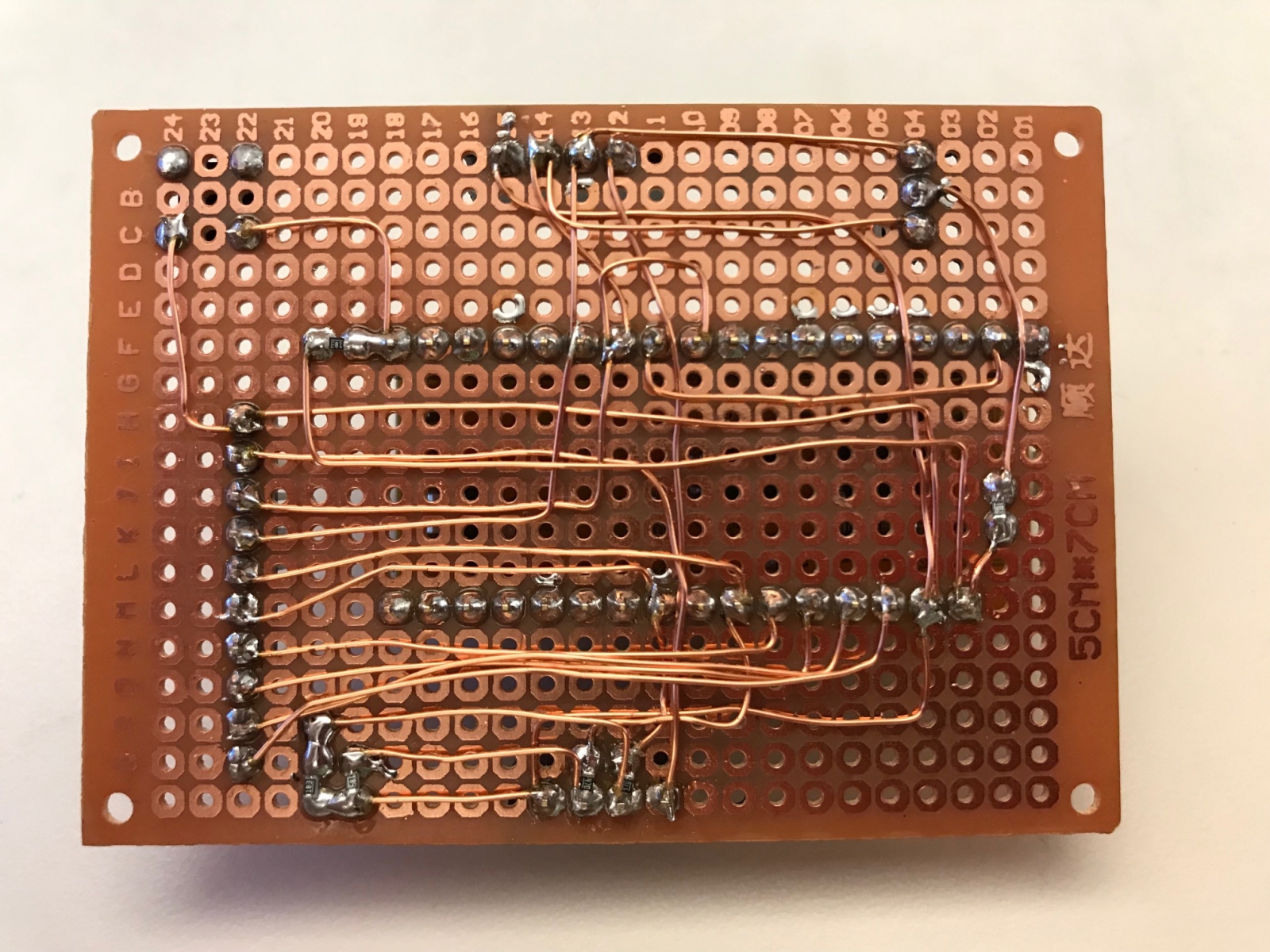
When manufacturing production volumes your CM isn’t going to use some solder wire and an iron instead, they’ll likely use solder reflow or wave soldering depending on the types of components in your design. The basics of soldering are the same whether you’re connecting wires to a speaker or SMT components to a PCB you’ll need solder, flux, and heat.
PCB SOLDERING SERIES
This series will give you a deep dive into the basics of soldering so you can understand how important it is in the manufacture of a good PCBA.
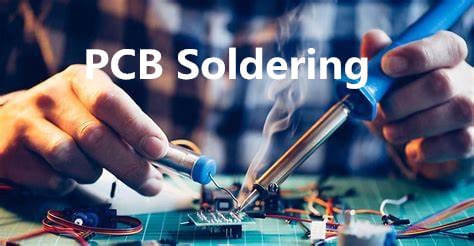
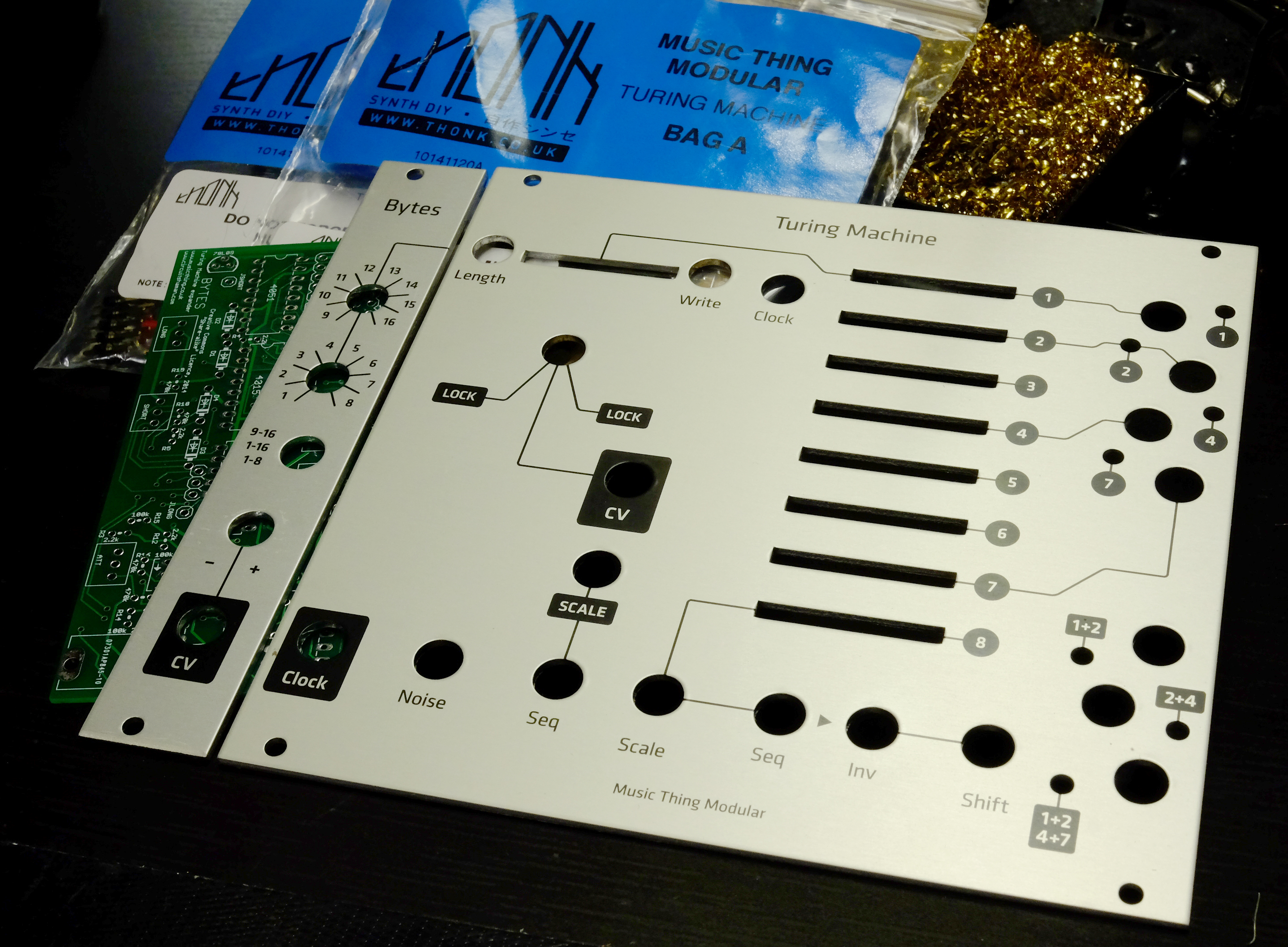
This kind of steep learning curve is even more prevalent in board design, where you have to learn the jargon to even begin to understand what a tutorial is talking about.
PCB SOLDERING HOW TO
In college, I had a lab where we had to solder two wires to a speaker and almost no one in the class knew how to do it. It’s often easy to take the basics for granted.
